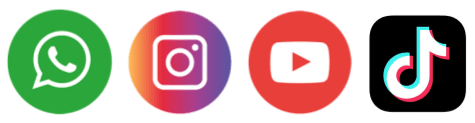
The 3 in 1 laser welding machine is an innovative device that combines welding, cleaning and cutting functions, perfectly solving the many challenges faced in traditional metal processing. Its welding function can efficiently join metals through a laser beam, and is widely used in precision welding tasks of various metal materials, whether it is thin plate welding or the connection of complex structures, it can easily cope with it. In terms of cleaning function, through precise laser beams, rust, oil, oxides, etc. on the metal surface can be removed, the surface quality of the metal material can be maintained, and better conditions can be provided for subsequent processing. The laser cutting function can quickly cut metal materials through high-energy laser beams, whether it is thin plates or thick plates, or even complex geometric shapes, it can be accurately cut to meet various processing needs.
The design of the 3 in 1 laser welding machine not only saves equipment space, but also reduces procurement costs and reduces the frequency of equipment maintenance and replacement, truly becoming an all-round equipment in modern manufacturing.

Future trends and industry impact of laser welding
- In modern industrial production, the widespread application of laser welding technology is driving innovation and change in the industry, especially in areas with high precision requirements such as automobiles and aerospace. Traditional welding methods often easily generate a lot of heat during the welding process, resulting in material deformation or uneven welds. Laser welding precisely controls the energy of the laser beam to make the welding area evenly heated, reduce the heat-affected zone, and effectively avoid material damage. In the automotive industry, the high efficiency and high precision of laser welding make body welding faster and stronger, especially suitable for welding thin materials in modern automobiles, and have strong market competitiveness.
- The manufacturing standards of the aerospace industry are much higher than those of traditional industries, and it places extremely strict requirements on welding technology. Laser welding technology is an ideal choice to meet these high requirements. It can not only efficiently weld high-temperature alloys and special materials, but also maintain the accuracy and strength of the welding points, ensuring the high performance and reliability of spacecraft parts. In addition, the high degree of automation of laser welding makes the production process more precise, reduces errors in manual operations, and improves overall production efficiency.
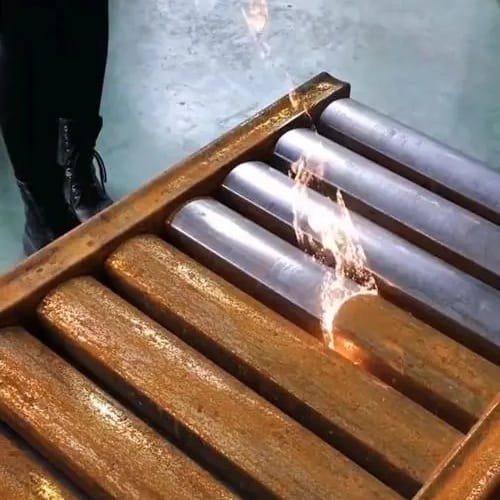
Laser cleaning: an efficient and environmentally friendly way to maintain equipment
- With the development of industrial technology, laser cleaning technology has gradually become an efficient and environmentally friendly equipment cleaning solution, especially when dealing with rust, oil stains and other substances on metal surfaces, showing significant advantages. Traditional cleaning methods often rely on chemical solvents, pickling or mechanical friction. These methods not only pollute the environment, but may also cause unnecessary damage to the metal substrate. Laser cleaning uses high-energy laser beams to irradiate metal surfaces, which can quickly evaporate or peel off contaminants such as rust and oil without damaging the metal substrate. Because laser cleaning does not require contact with the surface, it not only effectively protects the equipment, but also avoids the abrasion and chemical contamination issues that may be present with traditional cleaning methods.
- In terms of improving the surface quality of equipment, laser cleaning can restore the surface to a smooth and new look. For some industries with higher requirements, laser cleaning can remove stubborn rust or oil stains that are difficult to clean, ensuring that the equipment maintains good working condition during long-term use. For example, in the automotive and aerospace industries, the surface quality of equipment directly affects the performance and safety of the product. Regular laser cleaning can effectively extend the service life of the equipment and reduce the cost of maintenance and replacement parts. The popularization of laser cleaning technology not only optimizes the maintenance process of equipment, but also provides guarantee for the long-term operation of industrial equipment.
Laser cutting technology: crossing the boundaries of materials and thickness
- Laser cutting technology has become an important tool in the metal processing industry due to its high precision, rapidity and adaptability to different materials. The laser cutting function of the 3-in-1 laser welding machine can heat the metal surface with extremely high energy density by precisely focusing the laser beam, quickly melting or vaporizing it, and thus achieving cutting. The biggest advantage of this method is its cutting accuracy. Whether it is thin or thick plates, laser cutting can perform high-quality cutting with extremely small heat-affected zones, and almost no mechanical friction, avoiding material damage and precision errors in traditional cutting methods.
- For metals of different thicknesses and different materials, the application of laser cutting is very flexible. Thin metal plates can usually achieve very detailed and precise cutting, while thick metal plates can be cut quickly and ensure smooth edges. By adjusting the laser power, focus size and other parameters, it can adapt to the cutting needs of different metals, such as stainless steel, aluminum alloy, copper plate and other metal materials can be easily dealt with. The rapid processing capability of laser cutting greatly improves production efficiency, especially in industries that require high precision and fast delivery, such as electronics, aviation, and automobiles. The application of laser cutting technology provides companies with a strong competitive advantage.
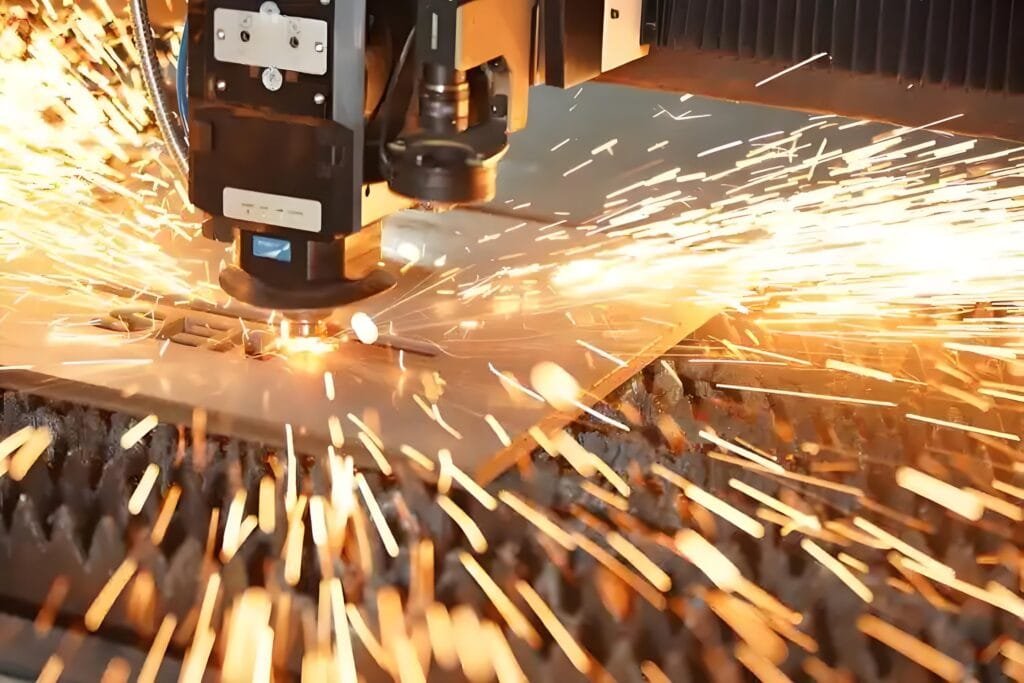
Optimizing production processes, three-in-one laser welding machines bring long-term benefits to enterprises
The 3 in 1 laser welding machine successfully optimizes the production process by integrating multiple functions such as welding, cleaning and cutting. Compared with the traditional division of labor operation, the three-in-one laser welding machine greatly shortens the production cycle and improves the connection efficiency between various processes. For example, during metal processing, laser welding and cutting can be performed simultaneously, while the cleaning function can promptly deal with contaminants on the surface of the workpiece to ensure seamless connection in each processing link. Through this integrated function, companies can significantly improve production efficiency while reducing changeover time between processes.
From a cost perspective, the 3-in 1 laser welding machine saves companies a lot of money by reducing equipment purchases, reducing labor costs, and reducing maintenance costs. The precise control of laser technology ensures the high quality of the processing process, reduces the production rate of substandard products, and reduces subsequent repair and rework work. Taken together, the three-in-one laser welding machine not only improves the company’s production efficiency, but also brings longer-term economic benefits to the company through cost optimization and resource saving.
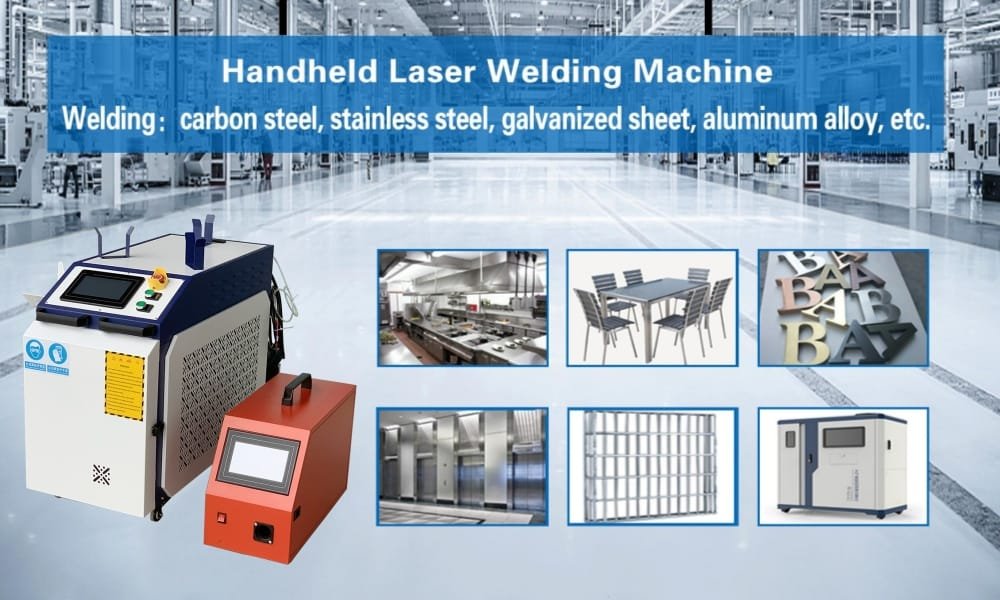