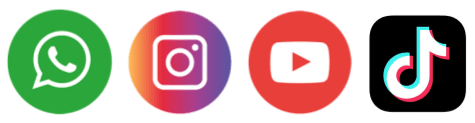
Laser Welding Technology, a cutting-edge process revolutionizing the field of metallurgy and thermoplastics, employs a laser beam to seamlessly join materials with unprecedented precision. This technology excels in both thin and thick materials, enabling high-speed welding in delicate applications and producing narrow, deep welds in robust structures.
Operational Modes: Conduction vs. Keyhole Welding
Conduction Limited Welding
In scenarios where power density remains below 10^5 W/cm2, conduction-limited welding takes center stage. Here, the laser beam’s energy is absorbed solely at the material’s surface, without penetrating it. The resulting welds often showcase a notable width-to-depth ratio.
Keyhole Laser Welding Technology
As laser welding transitions to higher power densities, surpassing 10^6-10^7 W/cm2, it adopts the keyhole mechanism. This involves focusing the laser beam to create a small spot, causing the material in its path to not only melt but vaporize. A cavity, termed a ‘keyhole,’ forms, filled with metal vapor or even ionized plasma. This innovative approach prevents the collapse of molten walls into the keyhole, allowing for unparalleled welding depth and precision.
Welding Process and Keyhole Dynamics
The keyhole, a crucial element in laser welding, contributes significantly to the welding process. It enhances the coupling of the laser beam with the workpiece, facilitating deep penetration welding. Traversing the keyhole along the joint or moving the joint relative to the laser beam achieves this, resulting in welds characterized by a remarkable depth-to-width ratio.
Surface tension plays a pivotal role in shaping the weld. Molten material at the keyhole’s leading edge flows around the cavity to the back, where it cools and solidifies, forming the weld. The distinctive chevron pattern on the weld cap points backward, capturing the dynamic journey from initiation to completion.
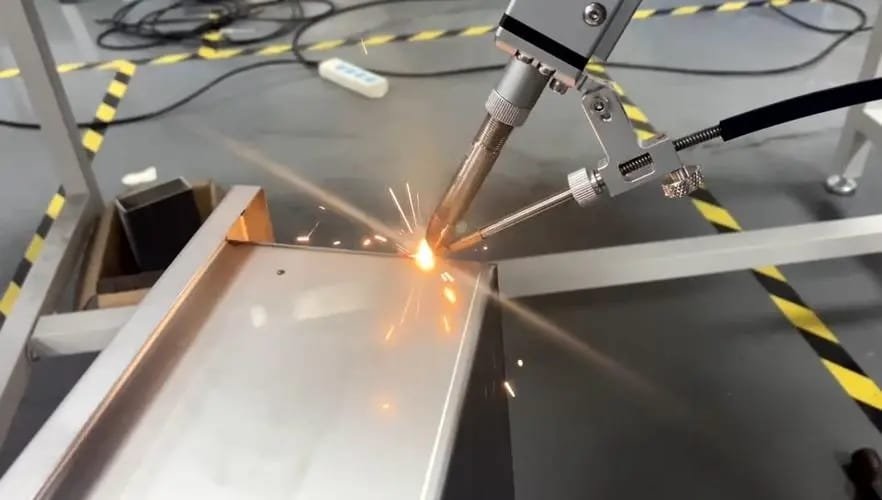
Applications and Advantages of Laser Welding Technology
Laser welding finds diverse applications across industries, from the automotive and aerospace sectors to medical devices, electronics, and even jewelry manufacturing. The technology’s advantages are manifold:
- Precision: Laser welding ensures meticulous welds with high accuracy.
- Speed: The concentrated energy of laser beams allows for rapid melting and minimal heat spread.
- Versatility: Capable of joining various materials, including metals, plastics, and ceramics.
- Quality: Produces high-quality welds with consistent mechanical properties and minimal defects.
- Automation: Easily adaptable to automated systems, ensuring precision and repeatability.
Challenges and Considerations
While laser welding offers groundbreaking capabilities, certain challenges and considerations exist:
- Material Limitations: Some plastics and ceramics pose challenges due to thermal and chemical reasons.
- Safety: Proper safety measures, including eye protection, are imperative due to the intense light and heat generated.
- Equipment Cost: Initial equipment costs can be high, potentially limiting accessibility for smaller businesses.
Conclusion
In conclusion, Laser Welding Technology stands at the forefront of modern welding techniques, pushing the boundaries of precision and efficiency. The dual modes of conduction-limited and keyhole welding, coupled with dynamic keyhole dynamics, showcase the intricacies of this innovative technology. With its wide-ranging applications and undeniable advantages, laser welding continues to reshape the landscape of manufacturing and engineering, promising a future defined by unparalleled welding precision and quality.
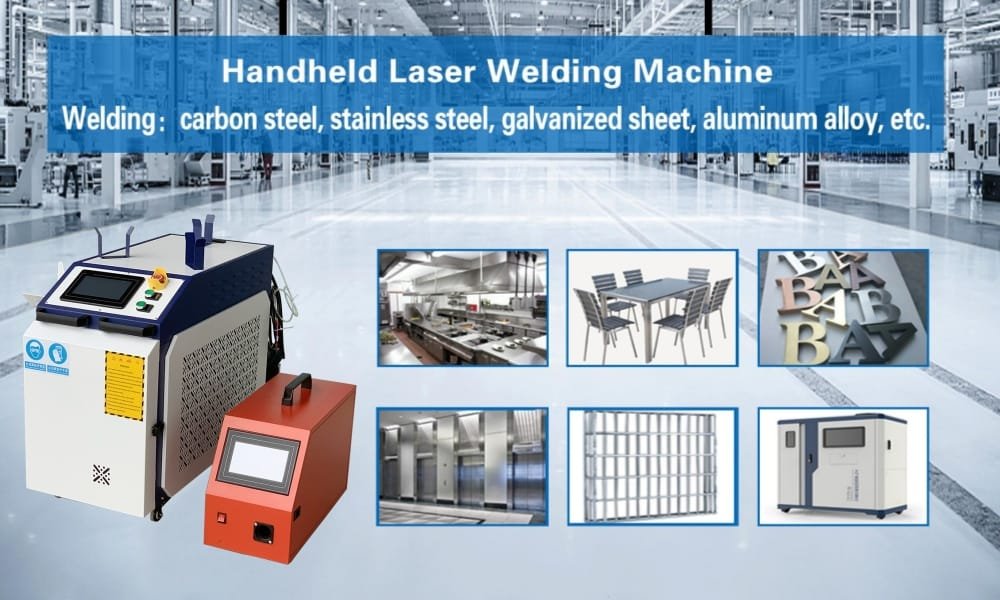