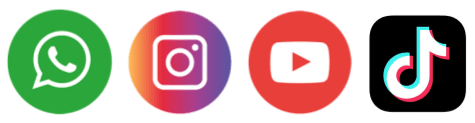
In modern aerospace, welding technology plays a critical role due to the need for precision and reliability. Aircraft, satellites, and rockets must endure extreme temperatures and high-intensity vibrations and pressures. While traditional welding methods have dominated aerospace manufacturing, advancements in handheld laser welding technology are revolutionizing the industry. Its efficiency, accuracy, and reliability make handheld laser welders essential tools in aerospace manufacturing.
This article explores several case studies of how handheld laser welding machines are used in different parts of aerospace, showing how they enhance welding quality and reliability while revolutionizing the field.
1. Welding of Aircraft Fuselage Structures: Combining Strength and Lightweight Design
The fuselage of aircraft and rockets must be both lightweight and strong. This often involves the use of materials such as aluminum alloys, titanium alloys, and high-strength stainless steel, which are lightweight but durable. Traditional welding methods, such as TIG (tungsten inert gas) or arc welding, often result in heat damage to these materials, weakening their structural integrity. Handheld laser welding machines, with their minimal heat-affected zone (HAZ), reduce material deformation significantly.
Case Study: Welding of Aluminum Alloy Fuselage Seams
Aluminum alloys are a primary material in aircraft fuselages. Due to aluminum’s high thermal conductivity, traditional welding methods result in significant heat dispersion, leading to stress concentration and material fatigue at the seams. Handheld laser welders focus high-energy beams precisely on the aluminum seams, minimizing the heat-affected zone and reducing deformation. Furthermore, the portability of handheld laser welders allows for flexible operation, especially in hard-to-reach areas of the fuselage, ensuring high-quality welds in difficult locations.
2. Welding of Aerospace Engine Components: Enhancing Heat Resistance and Fatigue Strength
Aerospace engines are the heart of any flying machine, operating in extreme conditions where temperatures can soar to thousands of degrees Celsius. The components of these engines must exhibit excellent heat resistance and fatigue strength. Handheld laser welding offers an ideal solution for manufacturing these parts.
Case Study: Welding of Titanium Alloy Blades
Titanium alloys are widely used in aerospace engines, particularly for turbine blades, due to their superior corrosion resistance, strength, and lightweight properties. However, titanium alloy welding is complex, and traditional welding techniques often result in cracks and porosity, affecting blade performance. Handheld laser welders allow for precise control of energy density, resulting in crack-free, high-quality welds. Since laser welding is a stable, spatter-free process, it ensures smooth, flawless surfaces, significantly increasing the durability of the blades.
Additionally, the portability of handheld laser welders offers significant advantages for the maintenance and repair of engines. In real-world engine use, components often require on-site repairs. Unlike bulky traditional welding equipment, handheld laser welders enable technicians to perform precise repairs directly inside the engine, minimizing downtime and increasing efficiency.
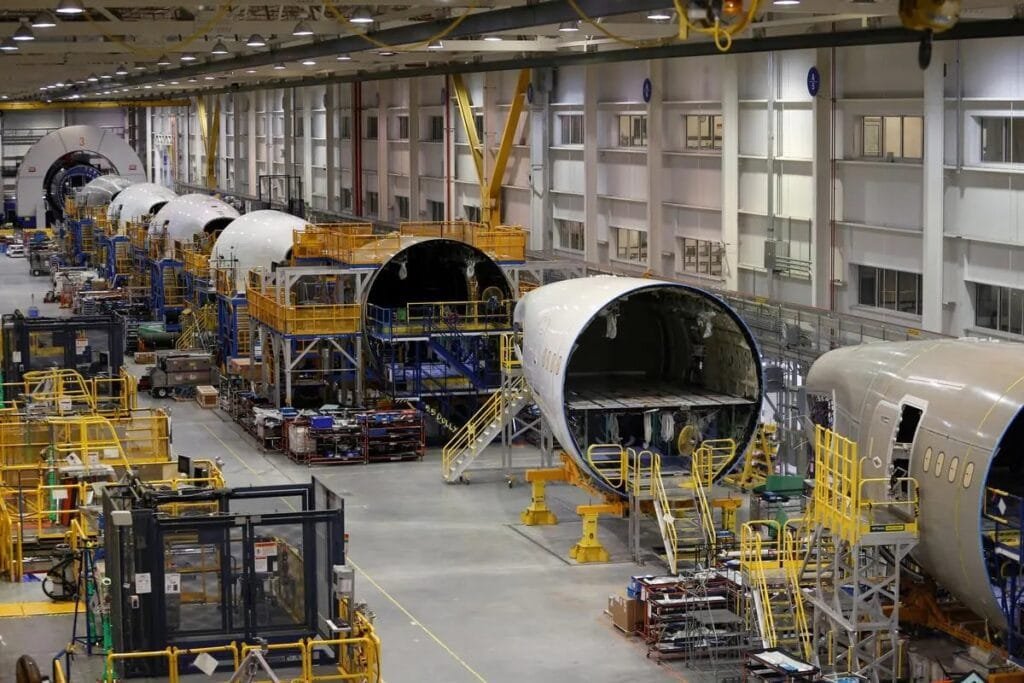
3. Welding of Satellite Structures: Ensuring Airtightness and Structural Integrity
Satellites, essential components of aerospace, must function in outer space, where they face extreme environments and must maintain perfect airtightness. Satellite structures are usually made from high-performance materials such as carbon fiber composites and aluminum alloys to withstand these harsh conditions. Handheld laser welding ensures that these materials retain their physical properties during welding while producing strong, seamless joints.
Case Study: Welding of Satellite Shells
Satellite shells must maintain airtightness in space, making weld quality crucial. Traditional welding processes often introduce high thermal inputs, resulting in stress concentrations and material deformation, compromising the satellite’s airtightness. Handheld laser welders, with their controlled heat input, focus energy precisely on the joint area, creating strong, pore-free, and crack-free welds. When repairing satellites, handheld laser welders allow operators to weld in tight spaces, providing a convenient, efficient solution for on-site repairs.
4. Welding of Aerospace Electronic Enclosures: Achieving High Precision and Performance
Aerospace electronic equipment often requires high-precision welding for enclosures to ensure electromagnetic shielding and reliable performance in extreme conditions. Handheld welding machines offer precise energy control and flexible operation, making them ideal for welding these critical enclosures.
Case Study: Welding of Nickel Alloy Electronic Device Enclosures
Nickel alloys are commonly used for aerospace electronic enclosures due to their corrosion resistance and electromagnetic shielding properties. Handheld laser welders can complete the welding process in a short time with high-energy density, producing smooth and visually appealing welds that ensure airtightness and effective shielding. Furthermore, the non-contact nature of laser welding prevents the heat damage to sensitive electronic components that can occur with traditional welding methods, ensuring the long-term stability of the devices.
5. Advantages of Handheld Laser Welding in Aerospace
Handheld welding machines offer several key advantages in the aerospace industry:
- Precision Welding: Welding’s ability to focus high energy enables precise welding, making it ideal for aerospace components with stringent seam requirements.
- Reduced Heat-Affected Zone: Compared to traditional methods, laser welding’s smaller heat-affected zone reduces material deformation and stress concentration, enhancing the lifespan of materials.
- Portability and Flexibility: The portability of handheld devices allows for easy movement, especially when welding complex parts or operating in confined spaces, significantly improving flexibility and efficiency.
- Efficiency and Cost Reduction: Laser welding is fast, and there’s no need for filler materials, which reduces welding costs while boosting production efficiency.
- Minimal Post-Processing: Laser welding produces smooth surfaces that typically require little to no post-processing such as grinding or polishing, saving time in production.
Conclusion
Handheld laser welding technology is revolutionizing the aerospace industry. Its precision and efficiency not only improve welding quality and reliability but also address many of the challenges posed by traditional welding methods. As handheld welding technology continues to evolve, its applications in aerospace will expand, providing higher efficiency and reliability in aerospace manufacturing for the future.
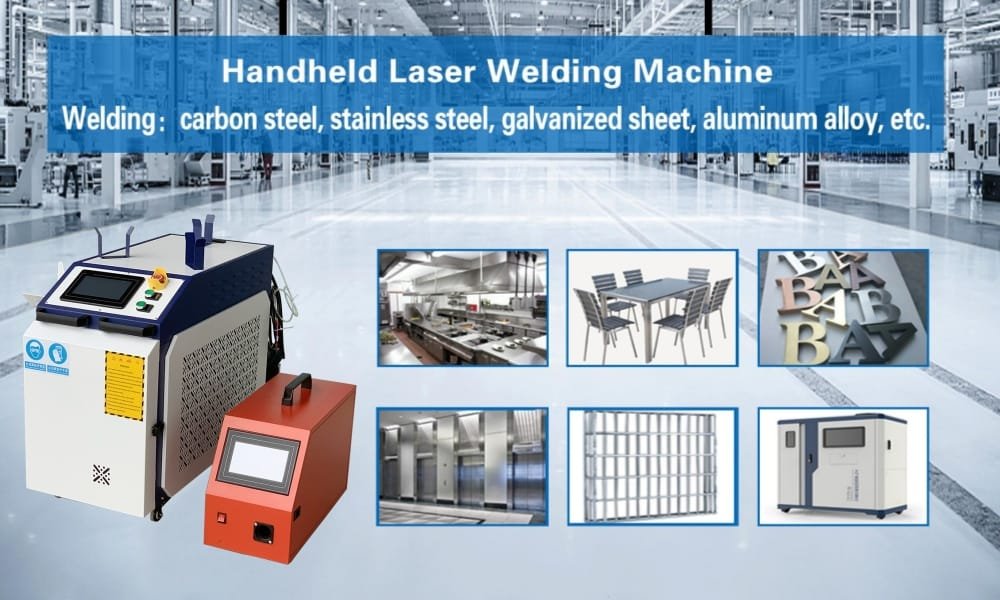