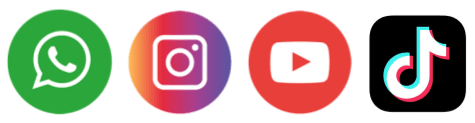
In the vast arena of modern manufacturing, welding technology is like a torrent that cannot be ignored, providing solid and reliable solutions for material connection in all walks of life. Among them, laser beam welding (LBW) has become a leader in the field of welding technology with its excellent precision and efficiency. However, traditional welding methods still have a place in the market due to their strong adaptability and cost-effectiveness. This article aims to explore the differences between laser beam welding and traditional welding technology in depth, helping you choose the most suitable welding method according to industry needs.
Understanding Laser Beam Welding (LBW)
1. What is Laser Beam Welding?
Laser welding, as the name suggests, is the use of highly focused laser energy beams to achieve material connection. This technology can generate high temperatures in a very small area, instantly melting and fusing metals. Laser beam welding is known for its high precision and low material deformation, and is a shining pearl in modern manufacturing.
2. Advantages of Laser Beam Welding
Ultra-high precision features:
Laser welding is known for its excellent precision, especially suitable for welding small parts or precision parts that require strict tolerance control (such as ±0.05 mm). This technology can ensure the fineness and narrowness of the welding part, accurately meeting the strict accuracy requirements of high-end manufacturing.
Deep penetration capability:
The laser has the ability to penetrate materials up to 20 mm thick, enabling deep welding while maintaining the smallness and beauty of the weld. This characteristic gives laser beam welding a unique advantage in the field of thick plate welding. Compared with traditional welding methods, its penetration depth can be increased by more than 30%.
Minimization of heat-affected zone:
The heat of laser welding is highly concentrated in a tiny area with a diameter of less than 1 mm, thereby greatly reducing the risk of material deformation (the amount of deformation can be reduced to less than 50% of traditional welding), and effectively reducing performance loss (strength loss less than 5%). This plays a vital role in maintaining the overall mechanical properties of the material and extending its service life, especially in industries with stringent material performance requirements, such as automobile manufacturing and precision instrument manufacturing.
Efficient production efficiency:
The laser welding process is extremely fast, the time to complete a single weld usually does not exceed a few seconds, and it is easy to integrate with automated control systems, making it extremely suitable for large-scale production environments. This efficient welding mode can significantly increase the output capacity of the production line (the production capacity can be increased by more than 30%), and effectively reduce the production cost (the cost is reduced by about 20%), bringing significant production efficiency and economic benefits to the enterprise. promote.
3. Limitations of Laser Beam Welding
Despite its many advantages, laser welding also has some limitations. First, the initial investment in laser beam welding equipment is high, which may be a considerable burden for small businesses. Second, some highly reflective materials (such as aluminum and copper) require special treatment during the welding process to avoid energy loss. Finally, the operation of the laser welding system is relatively complex, requiring professionals to perform precise parameter settings and operations, which increases the cost of learning and training.

What is the traditional welding process?
Traditional welding methods include arc welding, gas welding and brazing. We often use argon arc welding in daily life. For many years, it has been widely used in welding fields in different industries. Traditional welding has the advantages of low equipment cost, strong material applicability and easy operation, but it also faces challenges such as large heat-affected zone, low precision and slow speed.
Key Comparisons: Laser Beam Welding vs. Traditional Welding
1. Precision and quality difference:
Laser welding shines in high-precision operations, with clear and narrow weld lines. Compared to traditional welding, although the accuracy is slightly lower, it is still adept in situations where aesthetic and tolerance requirements are not high.
2. Material adaptability:
Traditional welding is good at handling various materials, including highly reflective metals, which often makes laser beam welding difficult. But in the production of high-strength alloys and defect free welds, laser beam welding has demonstrated superior performance.
3. Production speed and efficiency:
Laser welding has astonishing speed, especially on automated production lines, making it the preferred choice for high-yield industries such as automobiles and electronics. Although traditional welding has a slightly slower speed, it still holds a place in small-scale operations and maintenance fields.
4. Cost considerations:
Cost considerations: From an initial investment perspective, traditional welding has lower costs. However, the high efficiency and low waste of laser welding are sufficient to compensate for its initial investment in long-term large-scale production.
5. Convenient operation:
Traditional welding is easy to operate and does not require high technical requirements. Laser welding requires professional training to achieve optimal efficiency.
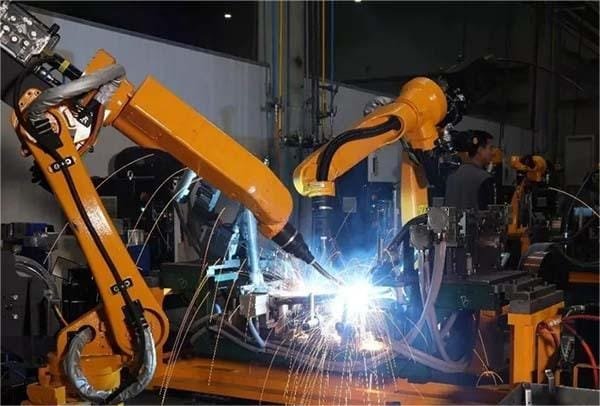
Industries Where Laser Beam Welding Can Be Applied
1. Welding of core parts in the automotive industry
Laser welding has the characteristics of high precision and high strength, making it the preferred welding technology for connecting key parts such as car bodies and doors.
In contrast, traditional welding processes are more used in the manufacture of large components such as frames and exhaust systems, showing their wide adaptability and cost-effectiveness.
2. Aerospace component welding
The aerospace industry has extremely high requirements for the strength and lightness of components, and laser welding is an ideal choice to meet these needs. It excels in manufacturing high-strength, lightweight components with its high precision and minimal deformation characteristics.
Especially when connecting thin-walled structures and complex components, laser beam welding shows its unique advantages.
3. Applications in Construction and Infrastructure
Laser beam welding is mainly used in the manufacture of steel structures, piping systems, doors, windows, and anti-theft nets in the construction and infrastructure fields. Its efficient and stable welding performance ensures the stability and safety of building structures. In addition, the flexibility and adaptability of laser beam welding enables efficient material processing and welding operations on site, improving construction efficiency and quality.
4. Application in Medical Device Manufacturing
The medical equipment manufacturing field has extremely high requirements for welding technology, and laser beam welding stands out with its high precision and clean weld advantages. It has become an ideal choice for manufacturing surgical instruments, implants, and precision medical equipment, ensuring that products meet the strict standards of the medical industry. The precise welding and clean welds of laser beam welding provide reliable quality assurance for medical equipment.
Choosing the Right Welding Method for Your Industry
The choice between laser beam welding and traditional welding depends on various factors, including precision requirements, production scale, material types, and budget constraints.
- Laser Beam Welding is ideal for industries requiring high precision, speed, and automation, such as automotive, aerospace, and medical manufacturing.
- Traditional Welding remains a reliable, cost-effective solution for construction, maintenance, and industries with less stringent precision requirements.
By understanding the strengths and limitations of each method, businesses can optimize their welding processes, improve product quality, and enhance overall productivity.
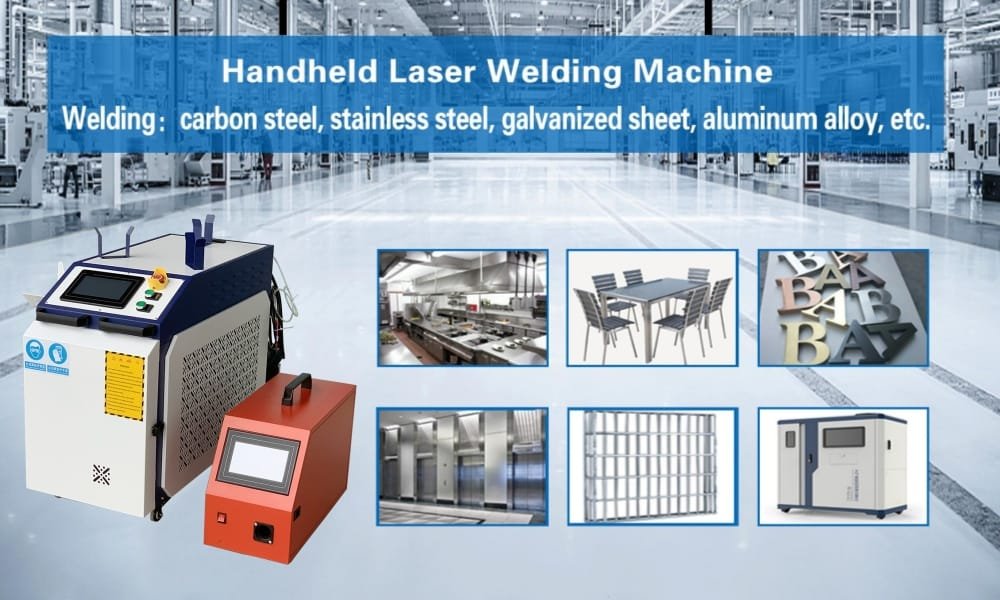