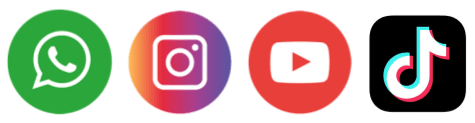
In modern industrial production, laser beam welder has become an indispensable equipment. Whether in automobile manufacturing, electronic component processing, or in aerospace, the applications of laser beam welding machines are constantly expanding. It not only improves production efficiency through high-precision and high-speed welding effects, but also greatly improves product quality and consistency. However, despite these advantages of laser beam welding machines, how to further improve welding efficiency in actual production is still an urgent problem that many manufacturing companies need to solve. Improving welding efficiency is directly related to the reduction of production costs and the improvement of productivity. By optimizing the welding process and increasing equipment utilization, downtime in production can be significantly reduced, thereby achieving higher output rates while maintaining high-quality welding. Therefore, improving the efficiency of laser beam welder has become a key task for the manufacturing industry in the fierce market competition.
Effect of material selection and pretreatment on the efficiency of laser beam welding machines
- When welding with a laser beam welder, the selection of suitable materials and effective pretreatment are crucial. The welding efficiency and quality of different materials vary significantly, which directly affects the accuracy of the welding results and the production cycle. For example, metal materials such as aluminum alloys, steel and stainless steel perform differently in laser welding. Aluminum alloys usually require higher laser power to achieve ideal welding results, while stainless steel due to its better thermal conductivity and weldability, Ability to complete welding at lower power.
- In order to reduce defects and errors during welding, pretreating the material is an essential step. Surface cleaning and removal of oil and oxides can significantly improve the strength of welded joints and reduce common problems such as pores and cracks. Through reasonable material selection and pretreatment, companies can not only improve the welding efficiency of laser beam welder, but also reduce material waste and production costs.
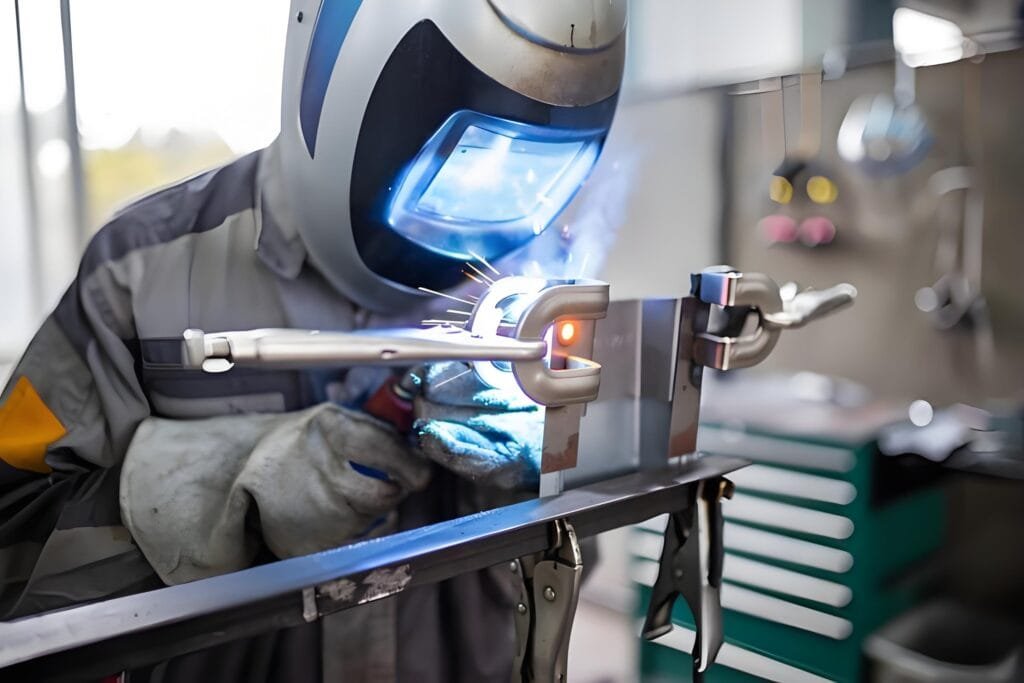
Accurately adjust laser beam parameters to improve welding production efficiency
- When using a laser beam welder, the parameter adjustment of the laser beam is directly related to the welding efficiency and the quality of the final product. The duration of the laser pulse is a key factor. Properly setting the pulse time can control the temperature change in the welding zone and prevent overheating or incomplete welding. For most metallic materials, shorter pulse durations generally help increase welding speed and reduce the material’s heat-affected zone.
- Power settings are also important parameters in welding operations. Appropriate power can achieve faster welding speeds, but too high power may cause excessive melting of the material or irregular welding joints. For thinner materials, the power can be appropriately reduced to avoid excessive heat-affected zones, thereby improving welding efficiency and accuracy. In addition, the focus size of the laser beam determines the fineness of the welding. Smaller focus points are suitable for high-precision welding, while larger focus points are suitable for larger ranges of welding operations. Through fine adjustment of laser beam parameters, production efficiency can be significantly improved without reducing welding quality.
Precise control reduces waste and improves welding accuracy
- When using laser beam welder for welding, it is crucial to reduce material waste and improve welding quality. Laser welding technology can reduce material waste by precisely controlling the heat input of the laser beam to avoid excessive melting and burning. During the welding process, the correct adjustment of the laser power, pulse frequency and focus size can ensure the heat concentration in the welding area and maximize the utilization efficiency of the material. For thin materials, excessive heat will not only waste raw materials, but may also cause deformation or welding defects. Reasonable setting of laser parameters can effectively reduce such problems and ensure that each weld joint is efficient and loss-free.
- To further improve the welding effect, quality control systems and real-time monitoring play an important role. In modern laser beam welders, they are usually equipped with automated monitoring systems that can analyze every detail of the welding in real time, including laser power, molten pool depth and temperature changes. Through these real-time data feedback, the system can automatically adjust parameters according to changes in the welding process to ensure welding quality and consistency. Through real-time monitoring and data feedback, not only the generation of waste is reduced, but also the strength and appearance of the welded joint are improved, making the entire production process more efficient and environmentally friendly.
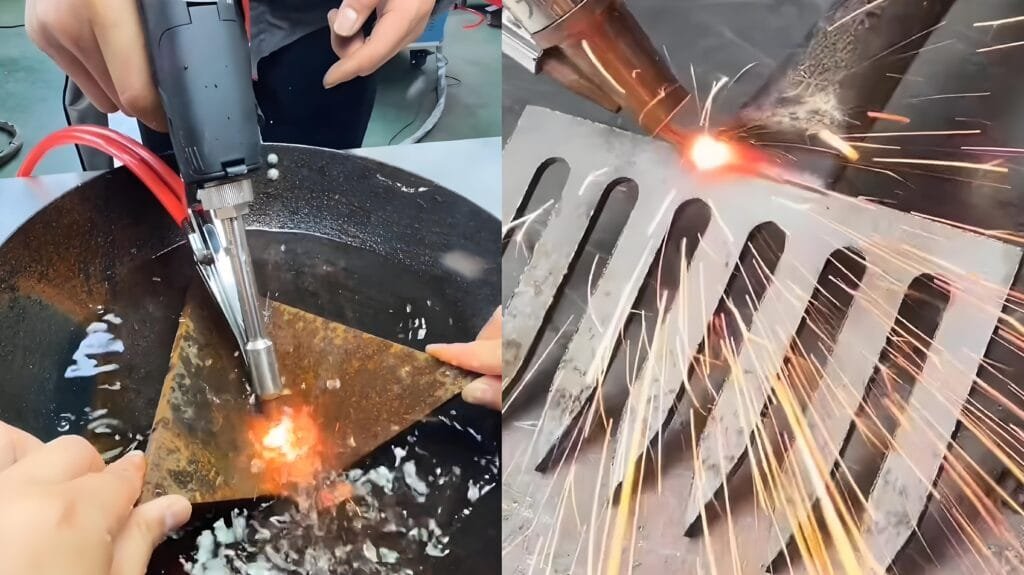
Improving welding quality, key steps for post-weld optimization
- Post-welding treatment is crucial when welding with a laser beam welder. Although laser welding can provide high precision and efficiency, it still needs to be properly optimized after welding to ensure the quality and reliability of the welded joint. First of all, the cooling process is one of the important steps in post-weld optimization. By properly controlling the cooling rate, stress concentration can be reduced and cracks or deformations caused by rapid cooling can be avoided. At the same time, proper surface treatment, such as removing oxide layers, grinding and cleaning, can also greatly improve the appearance of welded joints, ensuring they are flatter and smoother.
- Post-welding optimization not only helps improve welding quality, but also significantly reduces rework rates. Through reasonable post-welding treatment, repairs caused by welding defects (such as cracks and pores) can be reduced and overall production efficiency can be improved. When using laser beam welder, customized post-weld treatment methods are also particularly important for different materials and welding processes. Optimizing these links can not only improve product quality, but also reduce material waste, ultimately improving the company’s production efficiency.
Continuous optimization of welding processes to ensure increased productivity
When welding with a laser beam welder, optimizing the efficiency of every step is crucial. By selecting appropriate materials, accurately adjusting laser beam parameters, and strengthening post-welding optimization processing, welding efficiency and product quality can be significantly improved. Control of cooling speed, optimization of surface treatment and timely quality monitoring are all key steps to ensure welding effect and reduce rework. Continuously reviewing and adjusting these process links will help us discover potential improvement points and avoid waste and quality problems in the production process.
In order to achieve continuous improvement, welding operators and technical teams need to keep an eye on every aspect of the production line and evaluate the effectiveness of laser beam welding through data analysis and real-time monitoring. Regularly checking the performance and status of the laser beam welder and adjusting the welding parameters according to different material and process requirements can maximize its effectiveness. This continuous process improvement will help maintain a leading position in a highly competitive market environment, improve production efficiency and reduce costs.
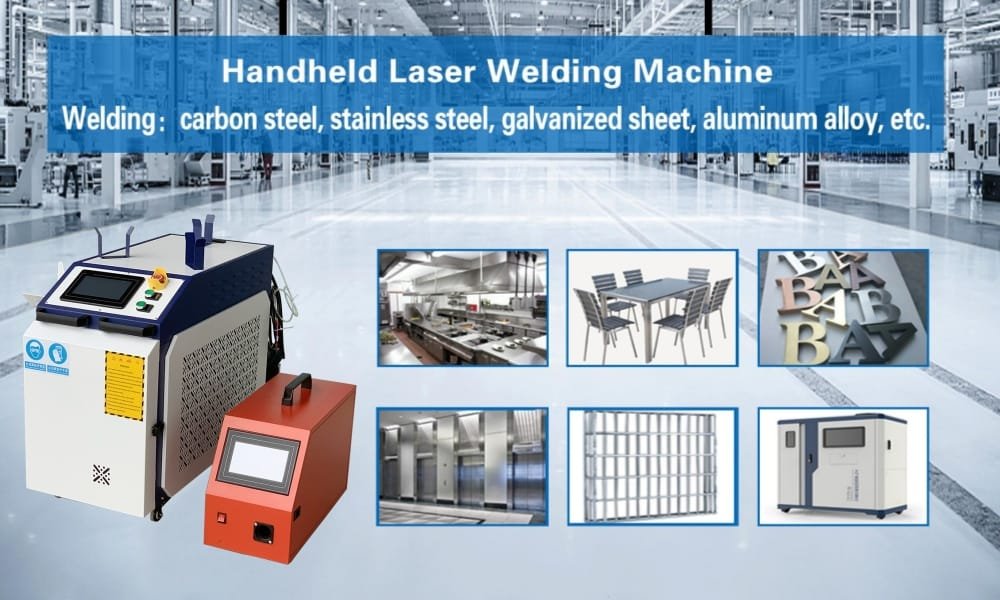