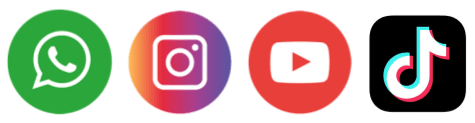
In recent years, laser welding technology has made significant advancements across various industrial fields, particularly in the electronics industry. Laser welding machines have become indispensable tools due to their high precision and efficiency. This article will explore the applications of laser welding machines in the electronics industry and showcase practical cases demonstrating their extensive use and remarkable advantages.
Basic Principles of Laser Welding Technology
Laser welding is a technique that uses a high-energy-density laser beam as a heat source to join materials. The primary principle involves generating high temperatures on the material surface through the laser beam, causing the material to melt rapidly and form a solid weld joint upon cooling. Compared to traditional welding methods, laser welding has several distinct advantages:
- High Precision: The laser beam can be focused on a very small area, enabling fine welding suitable for micro and complex components.
- High Efficiency: Laser welding is fast, with a small heat-affected zone, reducing deformation and thermal damage to the workpiece.
- High Automation: Laser welding machines can easily integrate with robots and automated production lines, enhancing production efficiency.
Applications of Laser Welding in the Electronics Industry
The electronics industry has stringent requirements for welding technology, especially with the trend toward miniaturization and high-density assembly. Laser welding technology, with its unique advantages, has been widely adopted.
1. Smartphone and Smart Device Manufacturing
In the manufacturing process of smartphones and smart devices, laser welding technology is extensively used to weld tiny components and enclosures. For example, Apple employs laser welding technology extensively in its iPhone production to connect the phone’s casing and internal components. Laser welding not only ensures the aesthetic and firmness of the weld points but also improves production efficiency and product quality.
2. Battery Welding
With the increasing demand for electric vehicles and portable electronic devices, the need for lithium batteries has surged. Laser welding machines play a crucial role in battery welding, particularly in welding battery tabs. Laser welding not only achieves high-strength connections but also ensures minimal thermal impact on the welded area, thereby protecting battery performance and lifespan.
3. Semiconductor Device Manufacturing
In semiconductor device manufacturing, laser welding technology is primarily used for packaging and connecting high-precision chips. Traditional welding methods can easily damage sensitive semiconductor materials, whereas laser welding can precisely control the heat, avoiding damage to the chips. Additionally, laser welding can achieve tiny weld points, meeting the high-density assembly requirements of semiconductor devices.
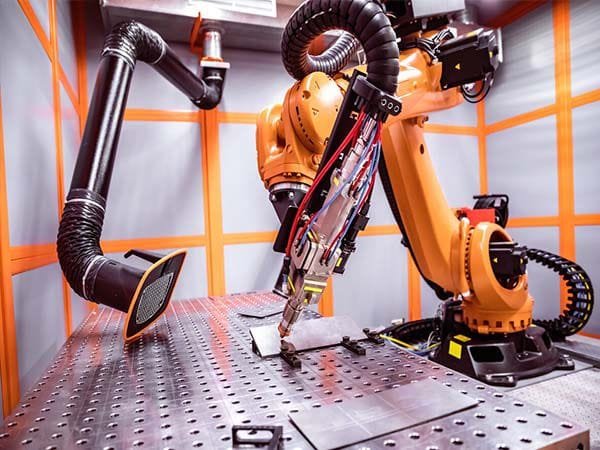
Practical Application Cases
Case 1: Application of Laser Welding in Smartwatch Manufacturing
A renowned smartwatch manufacturer introduced laser welding machines on its production line for welding the watch casing and internal circuit boards. The application of laser welding technology not only improved welding precision and speed but also significantly reduced production costs. With laser welding, the quality of the watch casing welds improved significantly, with aesthetic and firm weld points, ensuring the overall quality of the product.
Case 2: Laser Welding Technology in New Energy Vehicle Battery Welding
In the production of new energy vehicles, battery quality and safety are critical. A well-known new energy vehicle manufacturer uses laser welding machines for welding battery tabs. Laser welding technology not only achieved high-strength, high-reliability connections but also effectively controlled the heat-affected zone, preventing damage to battery materials, and enhancing the overall performance and lifespan of the batteries.
Case 3: Application of Laser Welding in Semiconductor Chip Packaging
In semiconductor chip manufacturing, a leading semiconductor company introduced laser welding machines for chip packaging. The high precision and efficiency of laser welding technology made the chip packaging process more accurate and reliable. The non-contact operation mode of laser welding avoided mechanical stress that traditional welding methods might cause, ensuring the integrity and performance of the chips.
Conclusion
With its high precision and efficiency, laser welding technology has been widely applied in the electronics industry. Practical cases have demonstrated its significant effects on improving product quality, production efficiency, and reducing costs. In the future, as laser welding technology continues to develop and innovate, its application prospects in the electronics industry will be even broader. Laser welding machines are not only key tools for electronics manufacturers to enhance competitiveness but also will lead the electronics industry into a new stage of development.
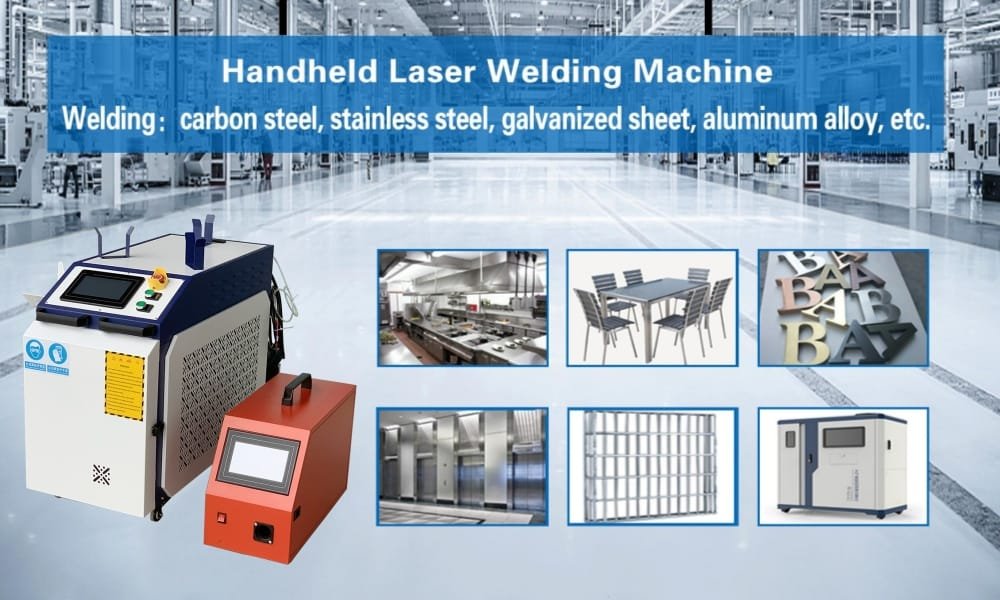