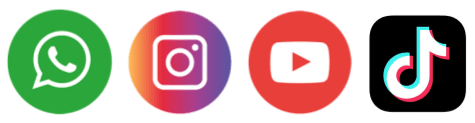
In manufacturing, molds are fundamental tools, responsible for shaping and forming products. Their quality and precision directly affect the final product’s success. With rising demands for accuracy and customization, the standards for mold processing have become stricter. Laser Engraving machines have emerged as valuable assets in this industry, offering unparalleled precision, contactless processing, and flexibility. This article explores the advantages of laser marking machines in mold processing, providing real-world applications that demonstrate how they achieve excellence in even the finest details.
I. The Advantages of Laser Engraving Machines in Mold Processing
Laser marking machines solve issues traditional marking methods face in precision, durability, and eco-friendliness. These machines bring several advantages to mold processing:
1. High Precision Marking
Laser marking machines offer micro-level precision, ideal for marking intricate patterns, small characters, and detailed logos on molds. This high accuracy ensures even the smallest details on mold surfaces are clear and precise, significantly improving mold quality.
2. Durability and Wear Resistance
Molds undergo extensive use in manufacturing, and laser-engraved marks are highly resistant to wear, corrosion, and fading. This durability makes laser marking ideal for molds used in high-stress environments.
3. Non-Contact Processing
Laser marking is a contactless process, meaning it doesn’t exert physical pressure on molds, preserving their original surface integrity. This is essential for precision molds, avoiding the wear-and-tear risks associated with traditional marking methods.
4. Flexibility and Automation
Laser marking machines can be programmed to change markings easily, accommodating various labeling needs, such as serial numbers, logos, or production dates. Many laser marking systems also support automation, enhancing production efficiency and consistency.
II. Real-World Applications of Laser Engraving in Mold Processing
Laser marking machines have found extensive applications across automotive, electronics, and medical sectors, which depend on molds for their products. Here are some real-world cases demonstrating how laser marking enhances mold processing.
Case 1: Precision Marking on Automotive Component Molds
An automotive component supplier adopted laser marking machines to engrave logos and part numbers on metal and plastic molds. Previously, traditional marking methods resulted in blurry and worn marks, diminishing brand visibility and traceability. Laser marking brought significant improvements:
- Clearer Brand Marking: Laser marking allowed precise engraving of brand logos on small mold surfaces, enhancing brand recognition and reputation.
- Wear Resistance: Even after repeated use, the markings remained clear, supporting traceability and quality assurance throughout the product lifecycle.
- Shorter Production Cycles: The high-speed efficiency of laser marking increased production by over 20%, meeting higher production demands.
Case 2: Micro-Engraving for Precision Electronics Molds
In the precision electronics industry, molds often require fine patterns and anti-counterfeit markings. One electronics manufacturer introduced laser marking to engrave complex security patterns on molds, enhancing product recognition and brand identity.
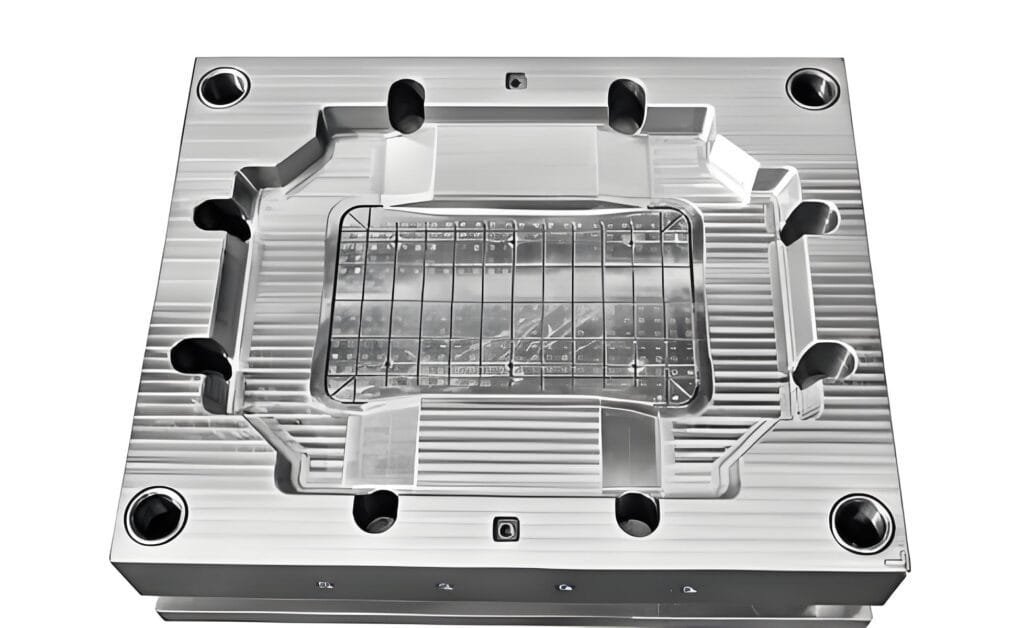
- Micro-Engraving Precision: Laser marking’s micro-engraving capability allowed for extremely detailed anti-counterfeit markings without damaging the mold’s structure.
- Enhanced Product Security: Each component produced carried a unique mark, effectively improving anti-counterfeiting efforts.
- Cost Savings: Laser marking replaced expensive labeling processes, reducing production costs while increasing efficiency.
Case 3: Batch and Serial Numbering for Medical Molds
In the medical device industry, mold processing often involves batch numbers and serial markings to support traceability. A medical device manufacturer integrated laser marking for mold identification, streamlining production and quality management.
- Efficient Traceability: Laser-marked batch numbers on molds provide a seamless tracking system, aiding in product identification and ensuring accountability.
- Reduction of Human Error: By automating serial number input, laser marking minimizes the risk of manual errors.
- Clear, Durable Marks: Laser marking produces sharp, permanent markings even on small mold surfaces, meeting the industry’s high standards for precision.
III. Achieving Precision and Quality with Laser Engraving Machines
Laser marking machines elevate mold processing by improving product clarity, durability, and environmental sustainability. Here are several ways these machines help the mold industry reach higher levels of precision:
- Enhanced Product Identifiability
Laser marking allows manufacturers to add distinct, recognizable features like logos and serial numbers to molds. This not only benefits the manufacturing process but also aids in post-production services like repair and maintenance. - Reduced Costs and Higher Efficiency
Laser marking’s non-contact process minimizes mold wear, extending mold lifespan and reducing replacement costs. Its fast processing time is particularly advantageous for high-volume production. - Flexible Marking with Programmability
Programmable laser marking systems allow manufacturers to adjust marking content as needed, streamlining the labeling process and supporting customization. Automated capabilities enable large-scale, consistent production. - Environmentally Friendly Processing
Laser marking requires no ink or chemicals, making it an eco-friendly solution. This aligns with the green manufacturing movement, supporting sustainable mold processing.
IV. Conclusion
Laser marking machines, with their high precision, durability, and environmental benefits, have become invaluable tools for the mold processing industry. Real-world examples from automotive, electronics, and medical sectors demonstrate how laser marking enhances quality and optimizes production processes. By adopting laser marking, the mold industry achieves superior product identification, improves efficiency, and meets modern demands for sustainability.
As laser technology continues to advance, its applications in mold processing are likely to grow further. Not only does it provide a reliable and efficient means of marking, but it also contributes to the mold industry’s overall quality and sustainable development, proving itself a vital tool in precision manufacturing.
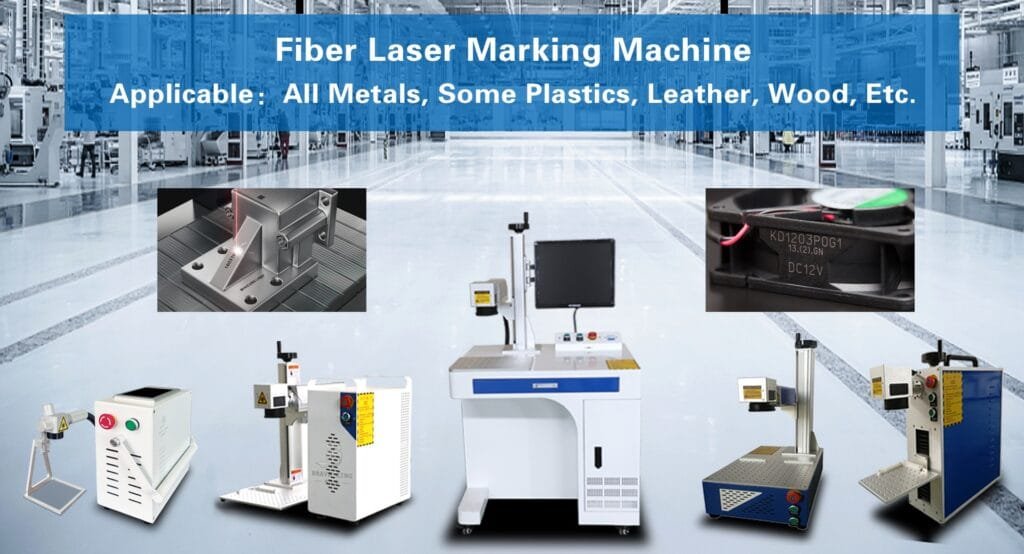