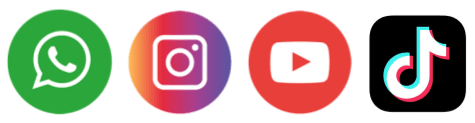
The aerospace industry has been relentlessly pursuing innovative technologies to enhance aircraft performance and safety. In this ever-evolving field, laser welding machines are emerging as a key player, injecting new vitality into aerospace manufacturing with their remarkable precision and efficiency. This article delves into the innovative applications of laser welding machines in aerospace manufacturing, featuring two compelling case studies.
1. The Miracle of Precision Connections
Critical components in aerospace often demand highly precise welding to ensure durability and safety. Traditional welding methods may fall short when facing complex aerospace structures, but laser welding machines, with their focused beams of light, can achieve precise connections for tiny and intricate components.
Case Study: Leading Aircraft Manufacturer
A renowned aircraft manufacturer introducedwelding machines to complete the assembly of aircraft engine components. Through laser welding, they achieved high-strength, damage-free connections, enhancing component longevity, and reducing the overall weight of the aircraft. This innovative welding method has garnered widespread attention in the aerospace industry, considered a milestone in improving manufacturing efficiency and aircraft performance.
Further Insights: Welding machines not only handle tasks beyond the capability of traditional methods but also provide unprecedented precision at the microscopic level. This miracle of precision connections not only improves the quality of aerospace components but also offers designers greater creative freedom.
2. Tackling the Challenge of Material Diversity
Aerospace manufacturing often requires welding different materials, such as aluminum alloys, titanium alloys, and more. Welding machines exhibit unique advantages in dealing with this diversity. Their high-energy-density beams can penetrate various materials, making the welding process more flexible while reducing the heat-affected zone.
Case Study: Laser Welding Advanced Aerospace Component Manufacturer
An advanced aerospace component manufacturer successfully employed welding machines to achieve composite welding of aluminum and titanium alloys. This innovation not only increased the overall strength of the components but also simplified the manufacturing process, reducing material waste. This successful case opens up new possibilities for the broader application of multi-material welding in the aerospace industry.
Further Insights: In the challenge of multi-material welding, welding machines, with their precise energy control, make connections between different materials more reliable. This brings greater flexibility and innovation to aerospace manufacturing.
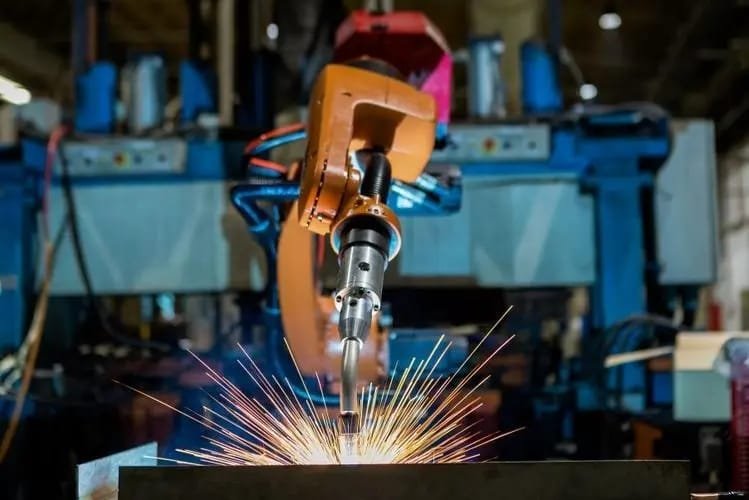
3. Efficient Production and Environmental Win-Win
The high-speed production and precise welding capabilities of laser welding machines not only improve manufacturing efficiency but also inject new environmental considerations. Traditional welding methods may generate waste and emit harmful gases, while laser welding machines reduce material waste and environmental impact during the welding process.
Case Study: Environmentally Conscious Aircraft Manufacturer
An environmentally conscious aircraft manufacturer introducedwelding machines, successfully reducing waste generation and minimizing harmful gas emissions during welding. This not only aligns with the company’s environmental philosophy but also earned them recognition through various environmental awards, showcasing their commitment to social responsibility.
Further Insights: The environmental advantages of welding machines lie in their non-contact nature and high energy efficiency, reducing material waste and improving resource utilization. This paves the way for sustainable development in the aerospace manufacturing industry.
Conclusion: A Bright Future for Laser Welding Technology
As an advanced welding process, laser welding machines are fundamentally transforming aerospace manufacturing. From precision connections to handling material diversity, laser welding machines offer a more efficient and reliable solution for aircraft production. With continuous technological advancements, we can anticipate more innovative applications of welding technology in the aerospace sector, painting a bright future for the industry.
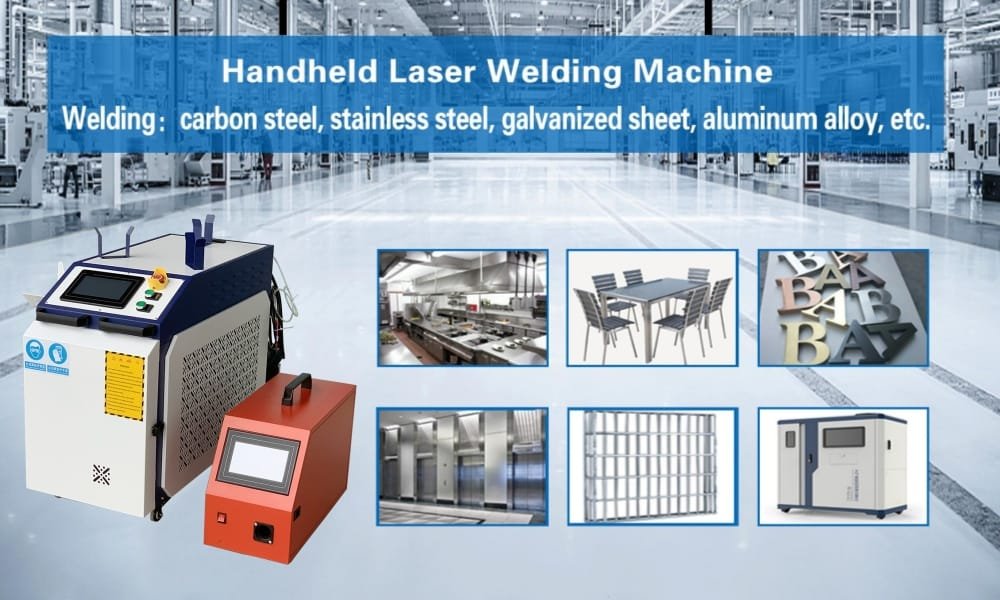