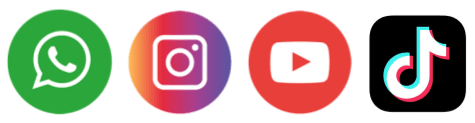
In the field of precision manufacturing, which requires high precision and efficiency, handheld laser welding technology stands out with its unique position. The emergence of this technology not only redefines the welding standards for precision manufacturing, but also brings revolutionary changes to many manufacturing industries with its unparalleled flexibility and efficiency.
The reason why handheld laser welder can occupy a place in the field of precision manufacturing is that it can achieve micrometer level welding accuracy, which is undoubtedly a huge blessing for product manufacturing that pursues ultimate quality and details. At the same time, this technology also has excellent flexibility and can easily meet the welding needs of various complex structures. Whether it is small electronic components or fine mechanical parts, handheld laser welder can easily complete welding tasks.
More importantly, the efficiency of handheld laser welder is remarkable. Compared to traditional welding methods, handheld laser welder can significantly shorten the welding cycle, improve production efficiency, and reduce energy consumption and material loss, bringing significant economic benefits to manufacturers. This efficient, precise, and flexible welding method is gradually becoming an indispensable technological force in the field of precision manufacturing, leading the manufacturing industry to a higher level of development.
Handheld laser welder: the future trend of efficient welding of precision components
Handheld laser welder technology has demonstrated unprecedented efficiency in precision component welding, completely overturning the complexity and inefficiency of traditional welding methods. By precise focusing of the laser beam, handheld laser welder can achieve fast and accurate welding of small components, with almost no preheating or subsequent processing required, greatly shortening the welding cycle.
This efficient process not only significantly improves production efficiency, but also enables manufacturers to complete more welding tasks in a shorter amount of time, thereby meeting the growing demand for precision components in the market. At the same time, the efficiency of handheld laser welder is also reflected in effective cost control. Due to the small heat affected zone of laser welding and minimal damage to materials, it can reduce material waste and lower production costs. In addition, laser welder has a high degree of automation, reducing reliance on manual operations and further lowering labor costs. In summary, the efficient process of handheld laser welder in precision component welding has brought dual improvements in production efficiency and cost control to manufacturers, promoting the transformation and upgrading of the manufacturing industry.
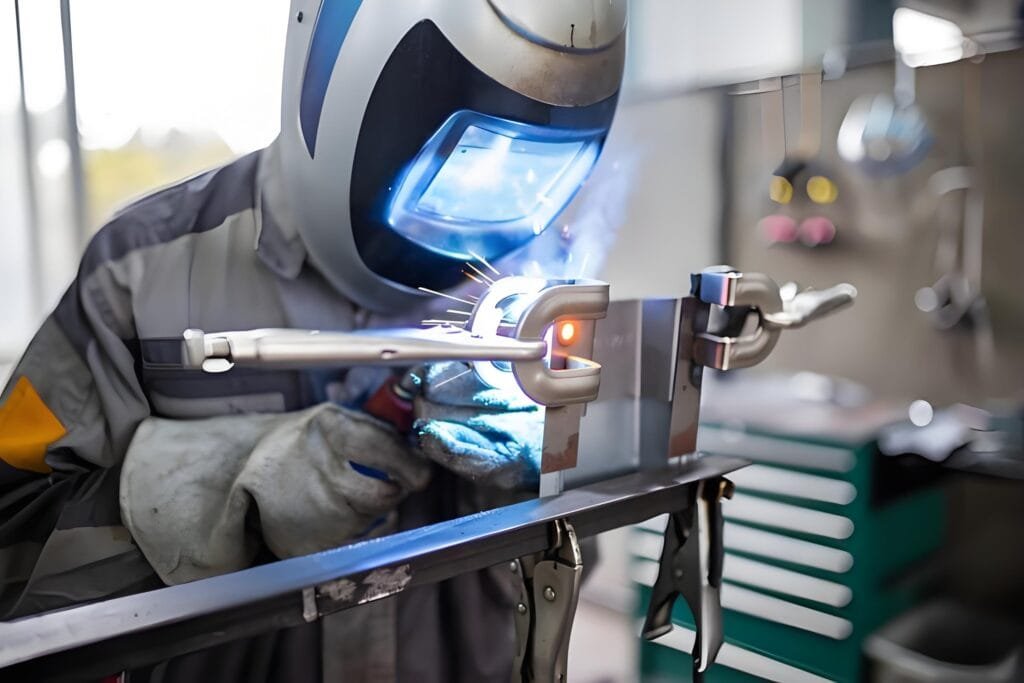
Handheld laser welder: an innovative solution for fine processing of complex structures
When facing welding tasks with complex structures, handheld laser welder provides a perfect solution for the manufacturing industry with its unique flexibility and innovative technical solutions. Traditional welding methods often struggle to achieve ideal welding results when facing complex structures, but handheld laser welder can achieve precise processing of complex structures with its precise laser beam control and advanced automation technology. Whether it’s welding seams in three-dimensional space or welding of small components, handheld laser welder can easily handle them, ensuring welding quality and accuracy.
The advantages of handheld laser welder are more prominent in ensuring welding quality and accuracy. The high energy density and precise focusing ability of its laser beam enable the welding process to quickly reach the melting point and form high-quality welds. Meanwhile, the heat affected zone of laser welding is small, causing minimal damage to the surrounding materials, thereby ensuring the overall strength and accuracy of the welded parts. In addition, handheld laser welder can also achieve automated welding and real-time monitoring through an intelligent control system, further improving welding quality and accuracy. These advantages enable handheld laser welder to not only improve production efficiency and reduce production costs when handling complex structural welding tasks, but also provide strong technical support for the transformation and upgrading of the manufacturing industry.
Solution to the welding challenge of special materials
In the field of welding, special materials such as high hardness alloys, high thermal conductivity materials, and composite materials pose great challenges to traditional welding techniques due to their unique physical and chemical properties. However, the emergence of handheld laser welder technology has provided new solutions for welding these special materials. Its unique advantage lies in the ability to precisely control the energy input during the welding process, thereby avoiding defects such as deformation and cracks caused by overheating of the material.
Handheld laser welder has demonstrated outstanding capabilities in solving welding problems. For high hardness alloys, laser welding can quickly reach the melting point, achieve high-quality welds, while reducing the heat affected zone and maintaining the original hardness and strength of the material. For high thermal conductivity materials, laser welding can quickly concentrate energy, reduce heat loss, and ensure the integrity of the weld and the performance of the material. In addition, for composite materials, laser welding can accurately control the heat input during the welding process, avoid thermal stress between different materials, and achieve good welding results.
Handheld laser welder also performs well in improving material performance. By optimizing welding parameters, laser welder can reduce defects such as porosity and inclusions in the weld seam, and improve the strength and toughness of the weld seam. Meanwhile, the cooling speed of laser welding is fast, which helps to form a fine grain structure and improve the overall performance of the material. These advantages make handheld laser welder the preferred technology in the field of special material welding.
Handheld laser welding: an innovative engine for precision manufacturing
In the field of precision manufacturing, handheld laser welder technology has demonstrated an irreplaceable and important position due to its high precision, high efficiency, and wide material adaptability. It can not only handle fine welding of complex structures, but also significantly improve material performance while ensuring welding quality, which is undoubtedly a huge blessing for the precision manufacturing industry that pursues ultimate craftsmanship and product quality. The introduction of handheld laser welder technology not only optimizes the production process and reduces costs, but also plays a key role in enhancing product competitiveness.
Looking ahead to the future, handheld laser welder technology will continue to evolve, and its level of intelligence and automation will be further improved. With the integration of advanced technologies such as artificial intelligence and the Internet of Things, handheld laser welder is expected to achieve more precise welder control, as well as real-time monitoring and feedback adjustment of the welding process. In addition, with the continuous emergence of new materials, handheld laser welder technology will also continue to expand its application scope, providing strong technical support for precision manufacturing in more fields. We have reason to believe that handheld laser welder will become a shining star in the field of precision manufacturing, leading the industry to a higher level of development.
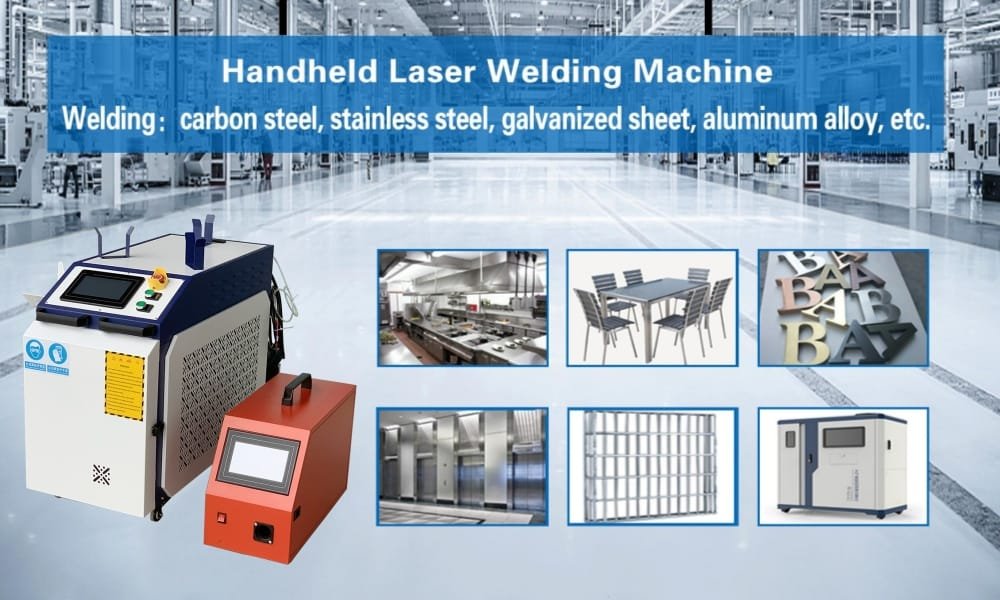