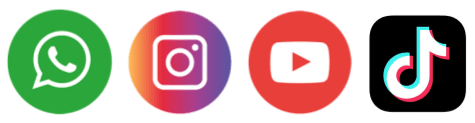
As industrial technology advances, the bearing industry faces increasing demands for product quality, traceability, and anti-counterfeiting measures. Laser marking machines have emerged as essential tools in precision marking, known for their accuracy, durability, and environmental friendliness. This article delves into how laser marking machines serve the bearing industry, emphasizing their benefits in precise engraving, adaptable marking sizes, and includes practical application cases that showcase how they significantly enhance product quality.
I. The Role of Laser Marking Machines in the Bearing Industry
Laser marking machines employ high-energy laser beams to engrave permanent markings on surfaces, widely applied for labeling product information, brand logos, batch numbers, and more on bearings. The clarity and accuracy of these engravings directly impact product quality and market reputation. Laser technology’s precision, speed, and versatility make it an ideal choice for marking in the bearing industry.
1. Durability and Wear Resistance
Laser markings are highly wear-resistant. Even in high-speed, high-friction environments, these engravings remain legible, supporting reliable product tracking and management.
2. Adaptability to Small Sizes and Fine Detail
Laser marking machines can engrave accurately on even the smallest bearing surfaces, such as those only a few millimeters in diameter, to mark brand logos, specifications, and security codes—tasks often difficult with traditional marking methods.
3. Efficiency and Eco-Friendliness
Laser marking is a non-contact, clean process that requires no consumables or additional chemicals, making it environmentally friendly. Its high marking speed also makes it ideal for large-scale production.
II. Adaptable Marking Sizes for Varied Needs
Bearing products come in a wide range of sizes. Laser marking machines are highly versatile, able to handle small, medium, and large bearings. They can engrave clear text and patterns on larger surfaces and can create fine engravings on small or micro-sized bearings.
Common Marking Applications by Size
- Large Bearings: For bearings over 50mm in diameter, laser marking machines can mark batch information, brand names, and other data in a prominent, legible manner.
- Small Bearings: For bearings under 5mm, laser markers can accurately engrave micro-codes and security markings, supporting brand authentication and product tracking.
- Micro Bearings: Even bearings around 2mm can be marked with specifications and anti-counterfeiting codes, ensuring that even the smallest parts are identifiable.
Laser marking machines’ flexibility allows companies to meet demands for both micro and large bearings.
III. Real-World Applications of Laser Marking in the Bearing Industry
In practice, laser marking machines have proven effective in various types of bearing marking tasks. Below are some real-world application cases demonstrating the advantages of laser marking in the bearing sector.
Case 1: Brand Marking on Automotive Bearings
An automotive bearing manufacturer uses laser marking machines to engrave brand logos and serial numbers on the outer rings of bearings. Previously, traditional marking led to blurred and worn-out marks, reducing brand recognition and product traceability. With laser marking, the text remains clear even in harsh automotive environments, enhancing both brand visibility and quality management.
Case 2: Anti-Counterfeiting on Small Precision Bearings
A precision instrument manufacturer sought to add anti-counterfeit marks on its small bearings to prevent counterfeiting. Laser marking machines enabled precise micro-engraving of QR codes and serial numbers on small surfaces, creating tamper-proof, traceable marks. This addition has bolstered the company’s product reliability and market reputation.
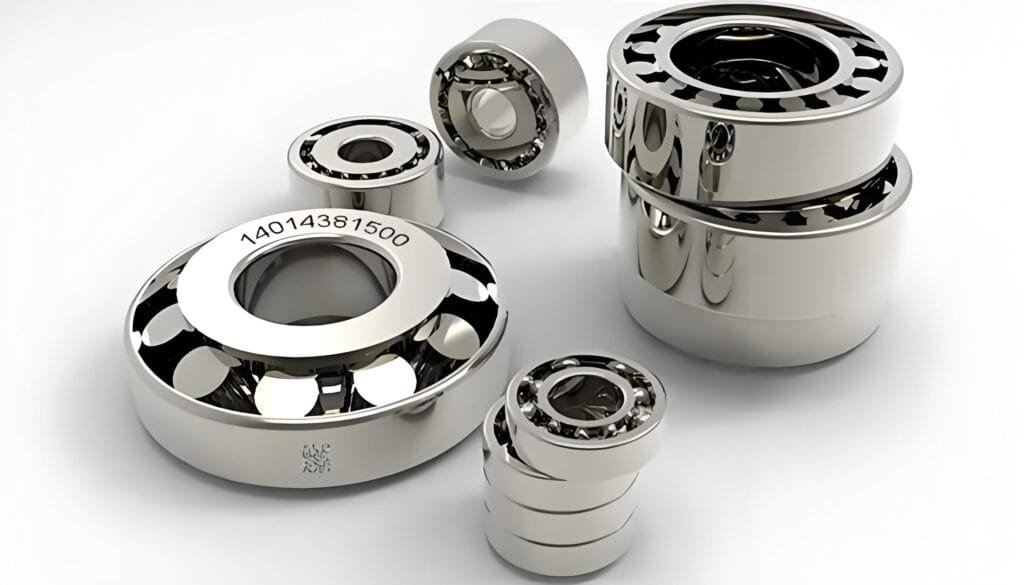
Case 3: Batch Management on Industrial Equipment Bearings
A major industrial equipment manufacturer uses laser engraving machines to engrave batch numbers and production dates on various bearings, enhancing inventory management and production tracking. The engraved information serves as a valuable reference for after-sales support, allowing service teams to quickly identify production details, boosting service response efficiency.
IV. Quality Improvements Enabled by Laser Marking Machines
By incorporating laser engraving machines, the overall quality and brand presence of bearings have significantly improved, with the following key benefits:
- Enhanced Traceability
Permanent markings, such as production batch numbers and dates, allow companies to trace product origins accurately, enabling finer control over quality and after-sales service. - Increased Anti-Counterfeiting Capability
Laser engraving supports flexible anti-counterfeiting measures by allowing detailed security engravings on bearing surfaces, effectively curbing the circulation of counterfeit products. - Improved Brand Recognition
Laser-marked logos and identifiers add clarity and durability, enhancing brand image. In sectors like automotive and aerospace, where product appearance matters, laser-marked bearings provide a professional edge. - Support for Diverse, Flexible Production
Laser engraving machines can handle various sizes and materials, supporting production needs from micro to large bearings. Quick content changes allow for responsive and flexible manufacturing.
V. Conclusion
Laser engraving machines offer unmatched precision, durability, and eco-friendliness, making them indispensable in the bearing industry. They meet the needs of varied bearing sizes, delivering precise, durable engravings that enhance brand recognition, traceability, and anti-counterfeiting measures. Practical application cases reveal how laser marking machines improve product quality and streamline production and service management.
As laser technology continues to evolve, its applications in the bearing industry are set to expand further. It is not only a tool for efficiency but also a pivotal factor in driving comprehensive quality improvements, making it an invaluable asset for the future of precision manufacturing in the bearing sector.
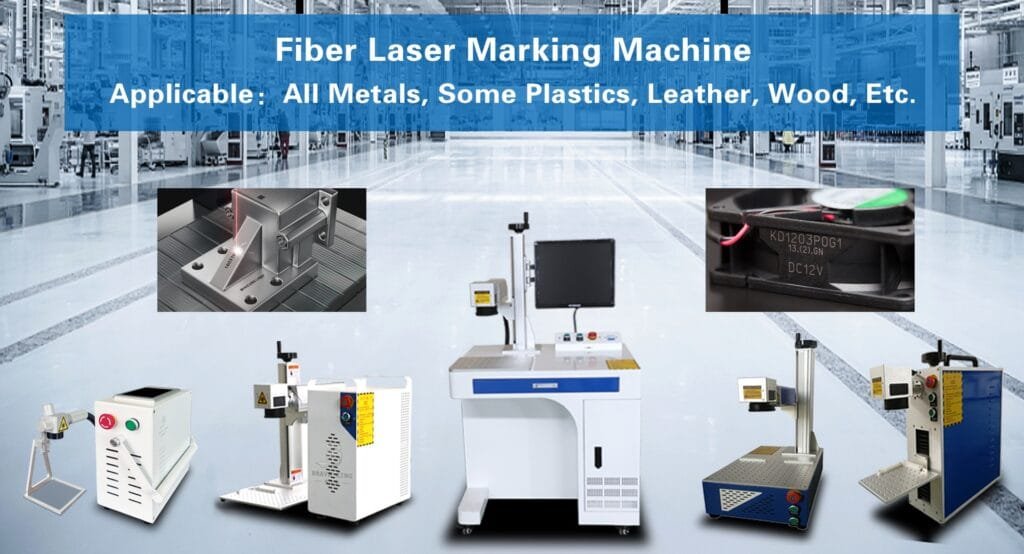