Your cart is currently empty!
Laser Welding Machines Make Jewelry Production More Efficient: The Future of Precision and Seamless Welding
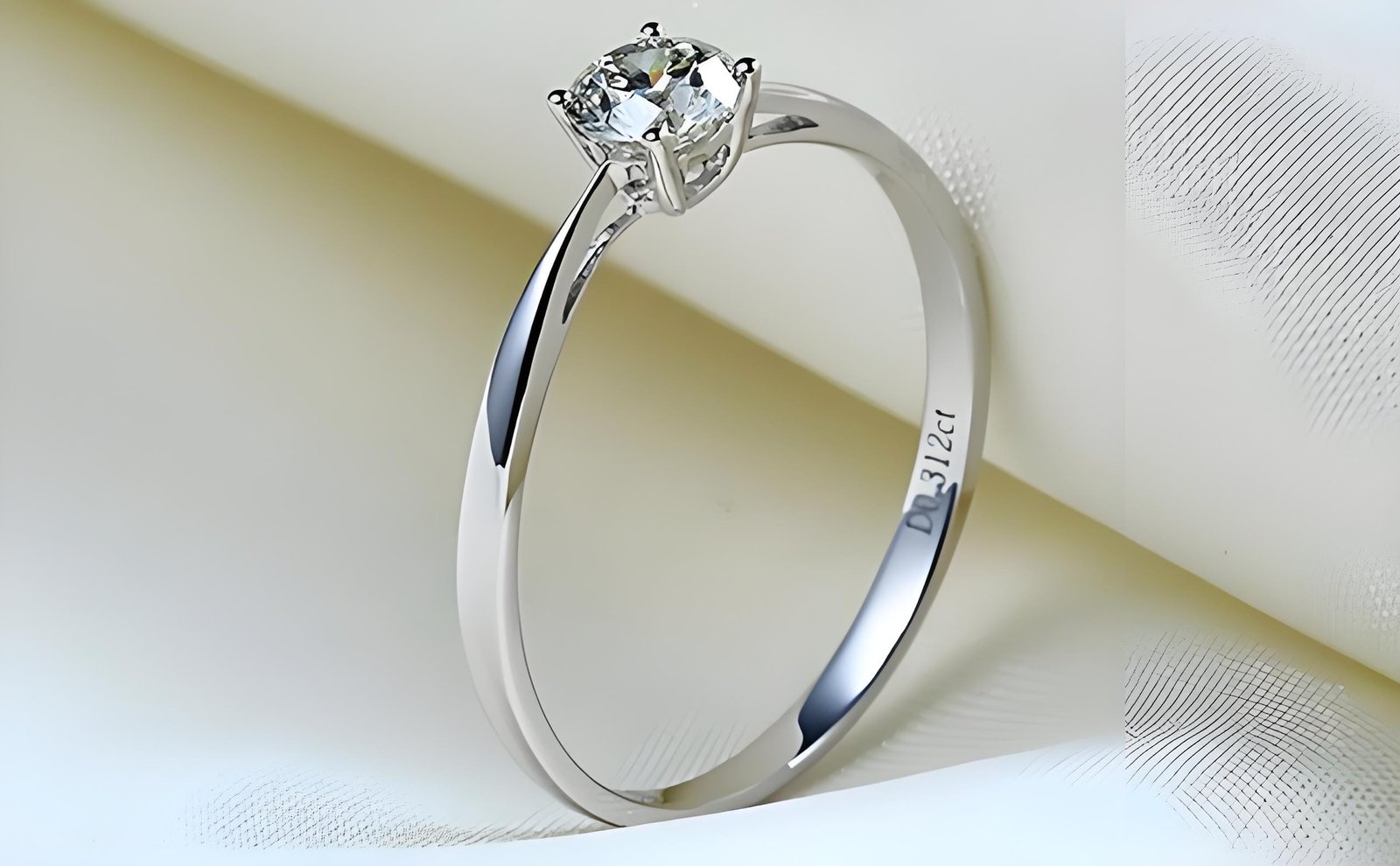
In the world of jewelry, where elegance and craftsmanship are highly prized, the production process behind each piece plays a vital role in achieving perfection. One crucial step in the manufacturing of precious metal jewelry is welding, which can significantly impact the product’s appearance and quality. Traditional welding methods often leave visible marks, require extensive post-processing, and pose challenges in working with delicate materials. However, laser welding machines are transforming jewelry production by offering precision and seamless welding solutions. This article explores how laser welding is making jewelry manufacturing more efficient and enhancing the overall quality of precious metal pieces through real-world applications.
1. The Rise of Laser Welding Machines in Jewelry Making
Laser welding machines are becoming increasingly popular in the jewelry industry, especially when working with precious metals like gold, platinum, silver, and white gold. The technology behind laser welding focuses a high-energy laser beam onto the metal surface, achieving a precise and controlled weld without causing significant heat-affected zones. This feature is particularly beneficial in jewelry making, where the materials are delicate, and aesthetics are paramount.
Compared to traditional welding methods, laser welding machines bring several key advantages to the jewelry industry:
- High Precision: They allow for highly detailed work, perfect for intricate designs.
- Minimal Heat Impact: Laser welding avoids deformation or discoloration by keeping heat confined to the welding area.
- Seamless Welding: The machines create clean, smooth welds with minimal to no visible marks, reducing the need for extensive post-weld processing.
2. Case Studies: Applications in Different Precious Metal Jewelry
To understand the real-world impact of laser welding machines, let’s examine some examples of how they are applied in different precious metal jewelry production processes.
Case 1: Welding Gold Rings
Gold, a soft metal, is commonly used in jewelry making but presents challenges during traditional welding due to its malleability and susceptibility to heat damage. For high-end gold rings, precision and flawless appearance are crucial. Laser welding machines have become essential in this domain, particularly when fusing ring components or attaching intricate embellishments.
- Precision Welding: Laser welding allows for accurate work in tiny areas, such as the inner bands of rings or settings for gemstones, ensuring seamless and invisible welds.
- Reduced Heat Impact: Traditional methods can cause gold to warp or discolor. Laser welding’s localized heat application prevents this, maintaining the material’s integrity.
- Minimal Finishing: With smoother welds, jewelers spend less time on polishing and post-processing, increasing productivity and reducing labor costs.
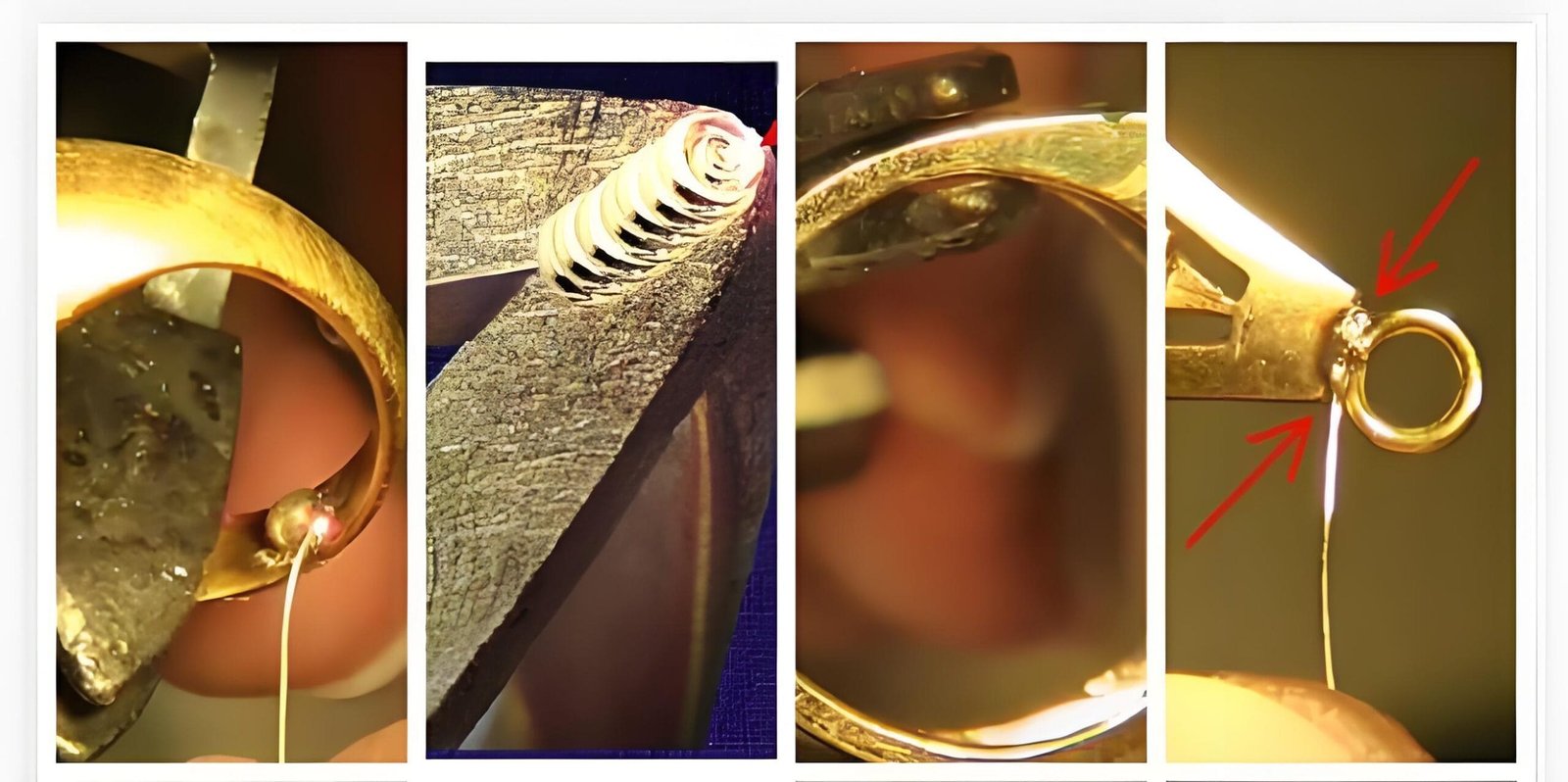
Case 2: Seamless Platinum Necklace Welding
Platinum, known for its hardness and resistance to oxidation, is favored in luxury jewelry. However, the very properties that make platinum desirable also pose challenges for traditional welding methods, often leaving noticeable weld marks or weakening the material. In intricate designs such as platinum necklaces, laser welding machines provide the precision needed to ensure durability and an impeccable finish.
- Seamless Joints: Laser welding creates nearly invisible joints, perfect for connecting fine platinum chains or intricate components of a necklace.
- Enhanced Durability: The controlled heat application of laser welding maintains the metal’s strength, ensuring the necklace is both durable and elegant.
- Flexibility in Design: Laser welding’s versatility allows jewelers to work with complex designs and ensure that every link or component is perfectly welded, offering more creative freedom.
Case 3: Repairing and Welding Silver Bracelets
Silver, a popular but challenging material in jewelry making due to its low melting point and tendency to tarnish, has long been problematic with traditional welding techniques. Laser welding machines offer an innovative solution for both creating new silver jewelry and repairing existing pieces.
- Precision Repairs: For repairing broken or worn silver bracelets, laser welding can focus on small areas without damaging surrounding material, ensuring the original design is preserved.
- Maintaining Shine: Traditional welding can cause silver to lose its luster. Laser welding’s controlled heat input helps maintain the metal’s original shine and finish.
- Damage-Free Repairs: For antique or heirloom silver pieces, laser welding provides a non-invasive method of repair, preserving the integrity and value of the item.
3. Analyzing the Production Process: How Laser Welding Enhances Efficiency
Beyond the aesthetic and material benefits, laser welding machines significantly streamline jewelry production, making the entire process more efficient. Here’s a look at how these machines transform key production stages:
1) Precision Welding for Intricate Components
Laser welding machines excel in precision welding, which is vital for handling intricate jewelry designs, such as gemstone settings or detailed metalwork in rings, necklaces, and bracelets. By focusing the laser beam on a minuscule area, welders can create strong, clean joints without affecting the surrounding material, ensuring both strength and beauty.
2) Strengthening and Securing Gemstone Settings
In gemstone jewelry, laser welding is invaluable for reinforcing settings and securely attaching metal prongs around the stone. The controlled energy output ensures the metal components are strong enough to hold the gem while maintaining the overall design’s delicacy and avoiding thermal stress on nearby stones.
3) Seamless Repairs for Heirloom Pieces
Laser welding machines offer an ideal solution for repairing or restoring antique and heirloom jewelry, where traditional welding might risk damaging fragile components. The precision of laser welding allows jewelers to fix issues such as broken clasps, chains, or settings without compromising the original design, extending the lifespan of these valuable pieces.
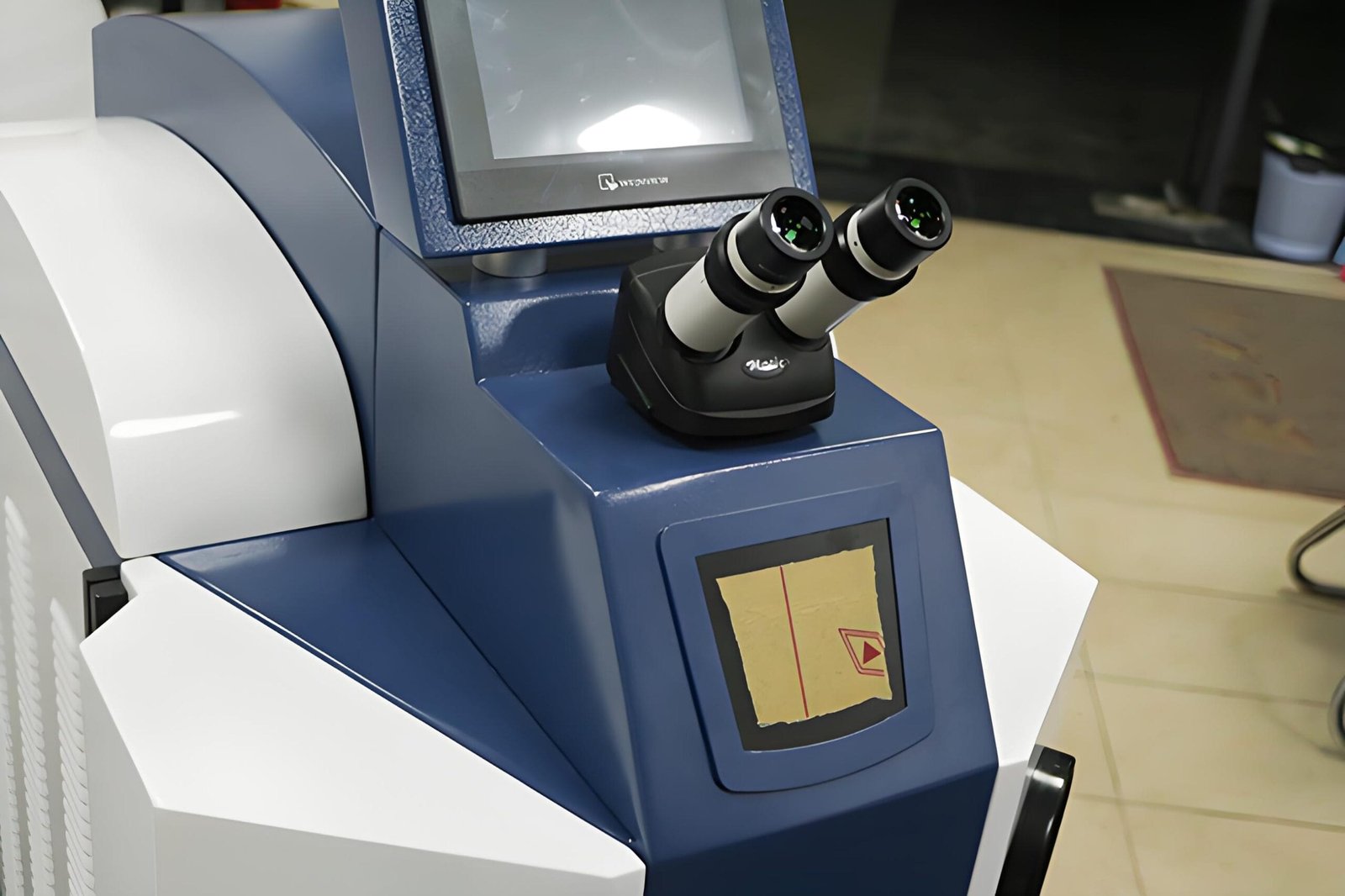
4. The Future of Laser Welding in Jewelry Manufacturing
As jewelry design continues to evolve, laser welding machines will play an increasingly critical role in production processes. Here are some trends and future directions where laser welding technology is likely to impact the jewelry industry:
1) Automation in Jewelry Production
With the integration of automation into jewelry manufacturing, laser welding machines could further improve efficiency by automating repetitive tasks such as chain-link welding or gemstone setting. This would allow manufacturers to increase production capacity while maintaining high levels of precision and quality.
2) Customized Jewelry
Laser welding machines allow for greater flexibility in working with personalized and custom designs. The precision and versatility of these machines enable jewelers to accommodate unique customer requests, such as intricate engravings, mixed metal designs, or custom-sized components.
3) Expanding Material Capabilities
As laser welding technology continues to improve, machines are expected to handle an even wider range of precious metals and metal alloys. This expansion will open new possibilities for jewelers to experiment with unconventional materials while still ensuring strong, high-quality welds.
5. Conclusion
Laser welding machines are revolutionizing the jewelry industry, particularly in the realm of precious metals. By providing precise, seamless, and efficient welding solutions, they help jewelers create more intricate, high-quality pieces while reducing production time and costs. Whether used for creating new jewelry or repairing treasured items, laser welding machines offer unparalleled advantages in terms of precision and aesthetic finish.
With continued advancements in laser welding technology, the future of jewelry making will undoubtedly see further improvements in both creativity and productivity. For jewelers looking to stay competitive and meet the demands of modern consumers, investing in laser welding technology is becoming not just an option, but a necessity.
Related Blogs
Portable Laser Engraver Machines: Become a Manufacturer of Unique Corporate Custom Gifts
Lighting the Path Ahead: Exploring the World of Laser Engraver Solutions
How to Choose the Right Laser Engraver Machine? Key Factors to Consider
Application and Innovation of Laser Engarving in the Tourism Industry
Leave a Reply